The Ultimate Overview to Welding WPS Procedures: A Comprehensive Review for Welders
In the complex globe of welding, Welding Procedure Requirements (WPS) work as the backbone of making sure high quality, uniformity, and security in welding procedures. Comprehending the subtleties of developing, implementing, and keeping an eye on WPS procedures is necessary for welders aiming to boost their craft and fulfill sector standards. As we explore the numerous parts of a WPS and discover the intricacies of qualification and certification, we will certainly uncover the essential duty these procedures play in the world of welding. Let's start a trip to untangle the intricacies and significance of WPS procedures in welding methods.
Value of WPS Procedures
Recognizing the relevance of Welding Treatment Specifications (WPS) treatments is vital for making certain the top quality and stability of welded frameworks. WPS procedures serve as a roadmap for welders, describing the required actions, criteria, and materials required to attain a sound weld. By sticking to WPS guidelines, welders can guarantee consistency in their job, leading to reliable and structurally audio welds.
One of the main reasons that WPS treatments are essential is their duty in keeping weld quality and honesty. Following the defined welding parameters and methods described in the WPS aids stop issues such as porosity, cracking, or insufficient fusion, which can compromise the stamina and resilience of the weld. Additionally, WPS treatments are important for making certain conformity with sector criteria and codes. By adhering to established WPS guidelines, welders can demonstrate that their work satisfies the needed requirements for safety and security and quality, providing guarantee to customers, examiners, and governing bodies. Fundamentally, the importance of WPS procedures can not be overemphasized, as they are fundamental to accomplishing regular, premium welds that fulfill market criteria and specifications.

Components of a WPS
A Welding Procedure Specification (WPS) commonly makes up important components that information the certain demands for executing a weld, guaranteeing consistency and top quality in the welding process. The vital elements of a WPS consist of vital variables such as base steels, filler metals, interpass and preheat temperatures, welding processes, securing gases, welding settings, and post-weld heat treatment demands.
Base steels describe the materials being signed up with, while filler metals are made use of to fill up the void between the base metals throughout welding. Preheat and interpass temperature levels are important for controlling the warm input and stopping problems like fracturing or distortion. The welding process outlines the details technique to be made use of, whether it's gas metal arc welding (GMAW), secured steel arc welding (SMAW), or another technique. Shielding gases secure the weld swimming pool from climatic contamination. Welding placements specify the alignments in which welding can be executed. Post-weld warm treatment may be needed to relieve stresses and improve the weld's buildings. An extensive understanding of these parts is important for producing a comprehensive and reliable WPS.

Credentials and Certification
Having established the necessary parts of a Welding Treatment Requirements (WPS), the emphasis now shifts towards the important facets of credentials and accreditation in welding practices.
:max_bytes(150000):strip_icc()/MIG20welding20arc20in20action-2000-e8844d72f5094d408b5ab6f1c9436a4f.jpg)
Certification, on the other hand, is the official acknowledgment of a welder's qualifications by a relevant qualification body or organization. Welding certifications are typically based on the specific welding procedures, materials, and settings a welder is qualified to deal with. Holding a valid welding qualification demonstrates that a welder fulfills sector standards and is qualified to perform welding jobs to the called for requirements.
Developing a WPS
To develop a Welding Procedure Requirements (WPS) that meets market criteria, mindful consideration of welding processes, products, and functional parameters is essential (welding WPS). The initial learn this here now action in producing a WPS is to determine the welding procedure to be made use of, such as gas steel arc welding (GMAW) or shielded steel arc welding (SMAW) When the welding procedure is determined, the next vital element is choosing the ideal materials, thinking about variables like base steel kind, density, and joint layout. Operational criteria such as welding current, voltage, traveling rate, and protecting gas structure have to also be diligently specified in the WPS.
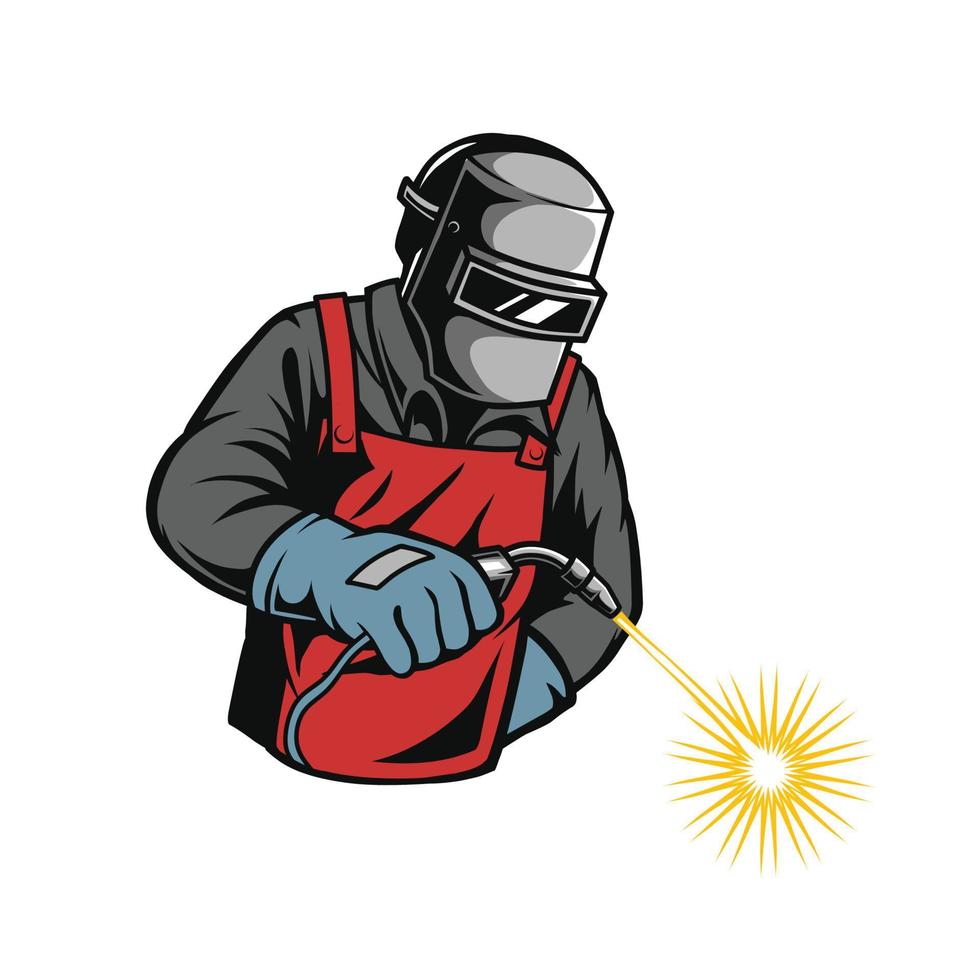
Applying and Keeping Track Of WPS
Upon finalizing the detailed Welding Procedure Spec (WPS) that diligently details welding processes, materials, functional criteria, and quality control measures, the emphasis moves to effectively applying and keeping track of the well-known procedures. Execution entails making certain that all welders involved in the project are acquainted with the WPS and follow it thoroughly throughout the welding procedure. This requires supplying ample training and guidance to ensure adherence to the defined treatments. Keeping an eye on the WPS includes continual oversight to validate that welding tasks align with the recorded requirements. Assessments, screening, and top quality control measures are vital elements of the monitoring process to determine any kind of deviations why not find out more or problems quickly. Regular audits and evaluations of the welding treatments aid in maintaining consistency and quality throughout the project. Efficient implementation and surveillance of the WPS are vital for guaranteeing the stability, stamina, and safety and security of the welded joints, inevitably adding to the total success of the welding task.
Final Thought
Finally, understanding and complying with Welding Procedure Specs (WPS) is important for welders to guarantee top quality, consistency, and security in their work. By recognizing the elements of a WPS, getting correct certifications and certifications, producing thorough treatments, and carrying out and checking them effectively, welders can enhance their skills and effectiveness in welding practices. Abiding by WPS procedures is vital for generating top quality welds and conference sector standards.
In the intricate world of welding, Welding Treatment Requirements (WPS) offer as the backbone of ensuring quality, uniformity, and security in welding procedures. The welding process describes the particular strategy to be used, whether it's gas metal arc welding (GMAW), shielded steel arc welding (SMAW), or one more method.To establish a Welding Procedure Requirements (WPS) that satisfies sector criteria, careful consideration of welding processes, products, and operational parameters is necessary. The first action in creating a WPS is to determine the welding process to be used, such as gas metal arc welding (GMAW) or shielded metal arc welding (SMAW)Upon settling the comprehensive Welding Procedure Requirements (WPS) that carefully details welding processes, materials, operational criteria, and top quality guarantee procedures, the emphasis moves to effectively executing and keeping track of the well established treatments.
Comments on “Advanced Welding WPS: Tailoring Specifications for Facility Tasks”